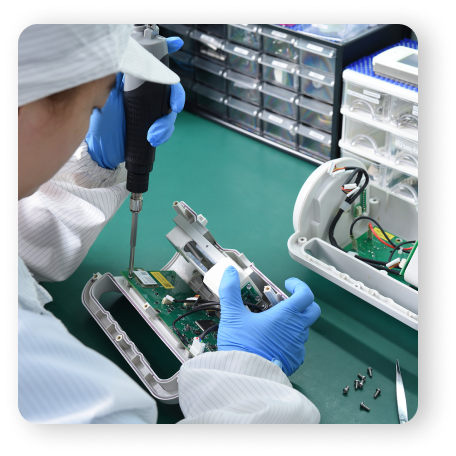

Enhance Your Medical Devices with Custom Components and Modules

Partnering with ACHB means gaining access to over 30 years of specialized experience in manufacturing high-quality components for the medical device industry. We leverage cutting-edge technology and deep industry insights to help your devices comply with regulatory standards and excel in performance.
Consult with Our Team of Experts
When you partner with experts who understand the medical device manufacturing landscape. From regulatory compliance to innovative design and rigorous quality testing, our specialized team is dedicated to delivering products that meet the highest industry standards for performance, safety, and efficiency.
Ensure compliance with essential regulations such as FDA and ISO 13485.
Streamline your workflows for increased efficiency and cost savings.
Implement advanced manufacturing techniques for enhanced device performance.
Consistent and dependable performance through standardized quality checks.
Compliance with FDA and international regulations.
Expert guidance to address complex design and production challenges.
Commitment to Quality Assurance and Testing
The performance and safety of your medical devices rely on rigorous testing and quality control. Our ISO 13485-certified systems ensure that your products meet all regulatory and performance standards. Our testing services offer:
Precision Manufacturing for
Medical Devices
ACHB crafts critical modules across a variety of medical applications, ensuring
precision and superior quality in every aspect of your device.
Fluid Modules Manufacturing
We specialize in creating precise solutions for fluid management systems, such as Infusion systems and Dialysis systems.
Fluid Modules Manufacturing
Detection Modules Manufacturing
Our capabilities extend to the development of smart detection systems, including Diagnostic devices and Patient monitoring sensors
Detection Modules Manufacturing
Innovative Automation Modules
We offer sophisticated automation solutions to enhance functionality and efficiency, including Surgical robotics and Automated drug delivery systems
Innovative Automation Modules
Temperature Control Modules Manufacturing
ACHB provides tailored solutions for precise temperature control, specializing in: Thermoregulation systems and Temperature monitoring sensors
Temperature Control Modules Manufacturing


Why Choose Us?

Experts In Component Design
By partnering with ACHB for your component design needs, you can ensure your designs are optimized for manufacturability, cost efficiency, and scalability, setting the stage for successful production and long-term performance. Contact our team to learn more about how we can support your next project.