Nothing is too complex.
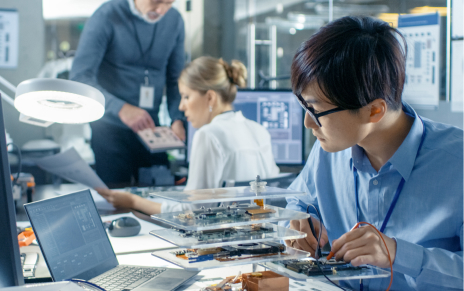
Medical Device Concept Development | ACHB
We create sustainable, FDA-compliant medical device products, reduce production costs, and accelerate time-to-market.
View Service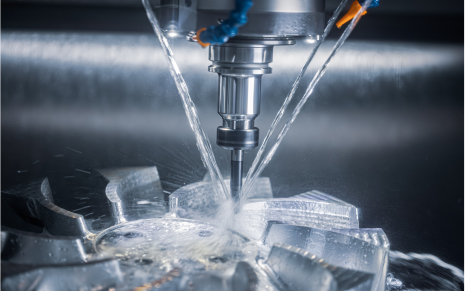
CNC Machining Capabilites
We deliver precision for complex geometries, ensuring compliance and optimizing production while cutting costs.
View Service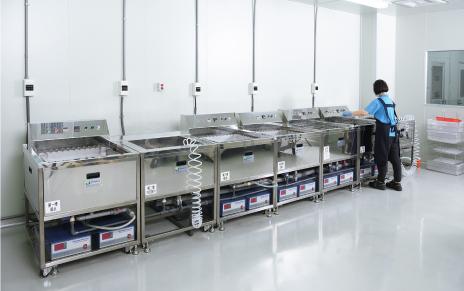
Additional Services
We test all products to ensure your products meet the highest standards of durability and efficiency
View Service

Why Choose Us?

Our reliable testing services ensure your equipment is durable, efficient, and ready to meet real-world challenges. Our mechanical, electrical, and biochemical testing expertise supports engineers in optimizing designs and enhancing system performance. Trust ACHB to deliver the reliability and support that helps ensure the success of your next project.