Reverse Engineering Atomic Absorption Spectroscopy Furnaces with ACHB
Atomic absorption spectroscopy (AAS) is a method used to analyze the concentration of a specific element in a sample. The process works by pumping the sample into a high-temperature furnace which causes the sample to atomize. A light source specifically tuned to the element being analyzed is shone through the atomized sample and the element will absorb that specific wavelength and become excited. The light spectrograph is then analyzed to determine how much light was absorbed, which is then related to the sample concentration.
The high-temperature furnace is a critical part of the AAS analysis system design. The furnace must be able to repeatedly heat a sample up to 2700°C in a few minutes and then cool it down to 2300°C, repeating this cycle three times to completely vaporize the sample.
An ACHB client, a manufacturer of AAS systems, became dissatisfied with the capabilities and support level of a long-term supplier of AAS furnaces. ACHB was able to not only take over the production of these furnaces but was able to do so at reduced cost and with improved productivity.
Challenges Faced by the Client
ACHB approached the manufacturer of this AAS equipment who at the time was struggling to find a reliable and transparent supplier of the furnace.
“The client was looking for someone who could do reverse engineering and find out what the specs were.”
Maggie Hsieh, VP Sales & Marketing / Sales & Marketing Dept
The manufacture of the AAS system furnace was relatively complex. It required multiple processes including machining, brazing, plating, and rigorous verification testing. The existing supplier of the furnaces had not provided the expected level of performance for a number of reasons:
- Increasing Prices:The original supplier regularly increased prices under the pretext of raw material price fluctuations. However, the price was never adjusted downwards when these prices dropped.
- Low Production:The client had an annual production volume requirement of 1,000 units, however, this target was often not met.
- Long Lead Time:The turnaround time from order placement to delivery was up to six months. Even so, agreements about delivery timing were not met.
- Specifications & Testing:Testing was performed behind closed doors and the client did not have direct access to the tests performed. Testing was also not performed in accordance with any industry-recognized standards, making it difficult to perform quality control on the parts.
“The client had no way to understand the quality requirements and had to just trust the supplier.”
- No Transparency:The original supplier kept the technology and their manufacturing methods in-house and as such made it difficult for the client to have complete control of the entire process. This put the client in the unenviable position of having to start from scratch if they decided to move to a new supplier. Ultimately, the original supplier took advantage of the fact that there were no other companies with the know-how to make the furnace components and did not share this information with the OEM.
“The client could not argue with the original supplier in terms of price or delivery dates.”
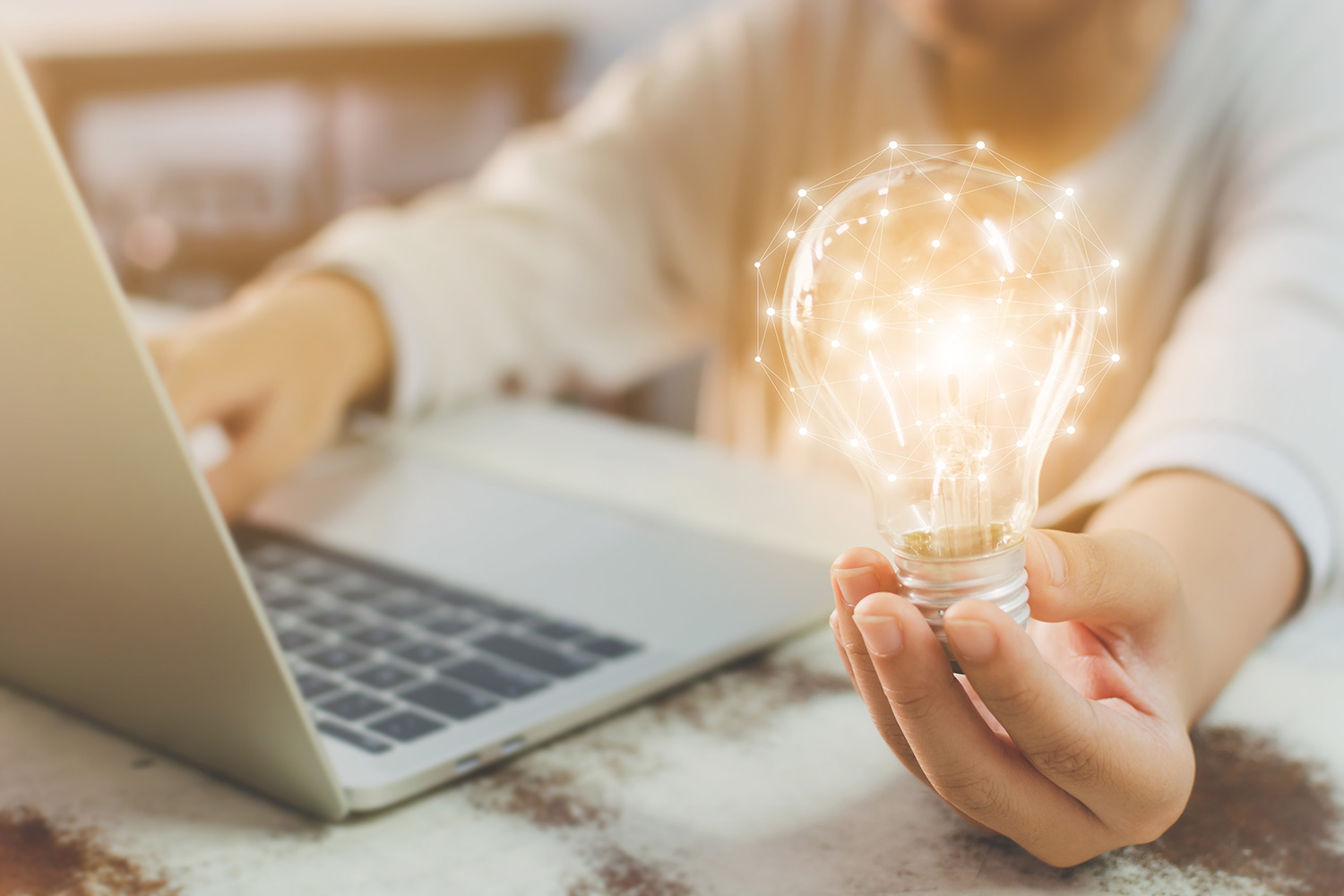
How Did ACHB Help?
In light of the challenges faced by the client, ACHB reached out and offered to not only manufacture these parts but also to become a technology partner with the client, adding value through:
- Reverse engineering:To manufacture the furnace components, it was first necessary to reverse engineer the equipment as lots of information was either lost or not shared from the existing supplier. ACHB was able to accurately measure the relevant components and develop a newly updated set of drawings that could be used to manufacture future parts.
“We have the knowledge to help our clients solve their issues.”
- Implementation of relevant standards:ACHB also manufactured the parts in accordance with relevant standards to ensure consistency and conformance.
- Process optimization:Through process optimization, ACHB was able to reduce the lead time from 6 months to 3 to 4 months.
- Improved productivity:ACHB helped improve productivity by helping the client not only achieve their original production requirements but exceed this by up to 20%.
- “The required annual supply volume was 1000 units, however, the client was unable to meet this as they could not control the delivery schedule and could only fulfill between 500 and 800 units”
- Significant cost-cutting:Through the above-mentioned increases in productivity and process automation, ACHB was able to significantly reduce the cost of the furnace.
ACHB’s proposal resulted in a multi-year vetting and qualification process which, in the end, produced a furnace that was less expensive, met the required specifications and could be manufactured at higher production volumes.
How ACHB Leverages In-House Expertise To Meet Client Requirements
ACHB has world-class technical know-how in terms of manufacturing components for advanced testing equipment and was, therefore, able to either directly produce or manage specialist subcontractors to ensure parts are manufactured to the relevant specifications. Some examples of the value added by ACHB are listed below:
1. Optimized Manufacturing Processes
The manufacture of the high-temperature AAS furnace requires a multi-step process that includes tube bending, machining, and brazing. ACHB was able to apply its extensive manufacturing and engineering expertise to not only re-create the processes implemented by the original supplier but also improve on them to reduce costs and increase production capacity.
- Tube Bending:Precise copper tube bending and brazing were required for the furnace coolant lines. Pipes had to be bent precisely to allow for enough clearance with existing parts to prevent any interference during assembly.
- Machining:ACHB's specialist knowledge in the field of CNC machining includes the development of machining fixtures to improve productivity, optimal tooling selection, and leveraging their extensive DFM (design for manufacturing) experience. This experience enabled ACHB to optimize machined part features, making them easier to machine. This, in turn, helped to reduce costs and improve efficiency. All of these factors combine to ensure consistent quality at a lower cost.
- Brazing:The various components of the furnace were to be joined using silver brazing. The brazed components were susceptible to thermal deformation as a result of being heated for brazing. It was critical to understand how much thermal deformation to expect to ensure that after brazing, the parts would still meet specifications. It was also important that the brazing did not negatively affect the quality of the subsequent plating as some areas' poor brazing meted the substrate which would create pockets and voids that could not be effectively plated.
2. Plating & Coating
The furnace inside an AAS system must be plated with various metals to improve thermal conductivity. These metals include copper, nickel, gold, and rhodium which are all plated on top of each other in the furnace. To achieve consistent thermal transfer performance from every furnace it's important to tightly control plating thickness. ACHB performed tests on older furnaces and was able to confirm that the plating applied was not only inconsistent but was also thicker than what was required which added cost to the furnace.
In order to determine the exact plating thickness on the parts, ACHB cross-sectioned a number of sample furnaces from the original supplier and measured the layer thicknesses with x-ray spectroscopy. ACHB discovered that the plating thicknesses were very inconsistent across the samples measured. The higher plating thickness significantly increased the overall cost of the furnace, as gold and rhodium are expensive plating materials. This excessive coating thickness contributed to the increased cost of the parts from the original supplier.
ACHB then invested significant time and effort to analyze the specific performance requirements of the furnace and proposed a plating strategy that precisely defined the plating deliverables to allow for effective quality control. ACHB optimized the plating thicknesses and was able to reduce them without negatively affecting the performance of the parts. This resulted in additional cost savings.
After plating, the parts were coated with PTFE (Polytetrafluoroethylene). However, in some cases, contamination present on the surface of the final rhodium layer would cause the PTFE to delaminate. ACHB developed a curing procedure that eliminated this problem and resulted in excellent adhesion.
ACHB was able to guide the plating subcontractor in order to maintain consistent results in accordance with ISO 9001 processes and procedures to ensure that overall cost was kept as low as possible without compromising the functionality of the furnace.
3. Quality Control, Testing & Assembly
Quality control and testing are critical for consistent part performance. The previous supplier was not transparent about their methods. For this reason, the client did not have confidence that the parts were fit for their purpose. ACHB implemented specification-backed quality control processes and test procedures.
- Quality Control:ACHB was able to implement and develop a range of applicable specifications to ensure traceability and product quality. The previous supplier specifically kept this information from the client and thus, it was never clear if the delivered parts actually met a relevant specification.
- Assembly:Assembling the furnace into the AAS machine had to be done in a very specific manner. This knowledge was not transferred to the client from the original supplier. Therefore, ACHB had to develop an SOP (standard operating procedure) to guide the client on how to effectively assemble the furnace. This helped increase assembly speed for the client and ensured that technicians installed all parts in a consistent manner.
- Testing:Testing during and after manufacturing was critical to ensuring that the furnace met the requirements of the relevant specifications. One particularly important type of test is to guarantee that the furnace gas and liquid cooling channels were well-sealed. ACHB developed a pressure and leak testing rig which was then distributed to subcontractors. The client also was given an identical testing machine so they too could perform the same tests and would not have to solely rely on a test report. This ensured that all subcontractors maintained the same high standards for testing and certification.
“The client now knows how to inspect the part as they have the machines, they know what to check, and they know what specification to follow”


Why Choose Us?

Why Partner With ACHB for Your Engineering Projects?
Clients can rely on ACHB to produce high-quality components through sound engineering practices and robust manufacturing, testing, and assembly procedures. ACHB has developed in-depth training regimens to ensure that all technicians and engineers are able to maintain company manufacturing standards. This allows customers the peace of mind and confidence to simply install manufactured components without having to be concerned about quality. To learn more about how we can leverage our extensive industry experience to assist you with your unique requirements, contact a representative at the link below.